As we all know, the product competitiveness and cost of an electric vehicle are determined mainly by the battery. Currently the mainstream is lithium-ion battery, and its technology has been developed for many years, but there have been no breakthroughs in electric vehicle applications. How so? At least so far, we have not seen a way to meet the needs of ICE cars owners in terms of manufacturing cost, energy density (range related), charging speed, or resistance to ambient temperature changes.
Having said that, as demand rises and economic scale continue to expand, the cost of manufacturing lithium-ion battery electric vehicles will continue to fall, catching up to ICE-equivalent levels around 2025 and even becoming cheaper than ICE vehicles by 2030. While it seems so promising, the supply of the precious metal in this battery, cobalt, has been unstable in the DRC in Africa, the world's largest supplier of this metal, due to years of war. Some companies then began to study the feasibility of reducing the share of cobalt used while increasing the nickel share, but this approach's effect is limited. The latest breakthrough research uses silicon to replace the graphite electrode material. Silicon has 25 times the linkage capacity of graphite for lithium ions and can increase battery energy density by 20-30%, charge eight times faster without compromising battery performance, resist temperature changes, and have a longer life and even lower cost. The new technology has recently overcome the issue about silicon particle volume changes, which causes too much rupture, resulting in the gradual decline of battery performance. At first, this new technology may be used in the newest mobile batteries, so we will see what happens.
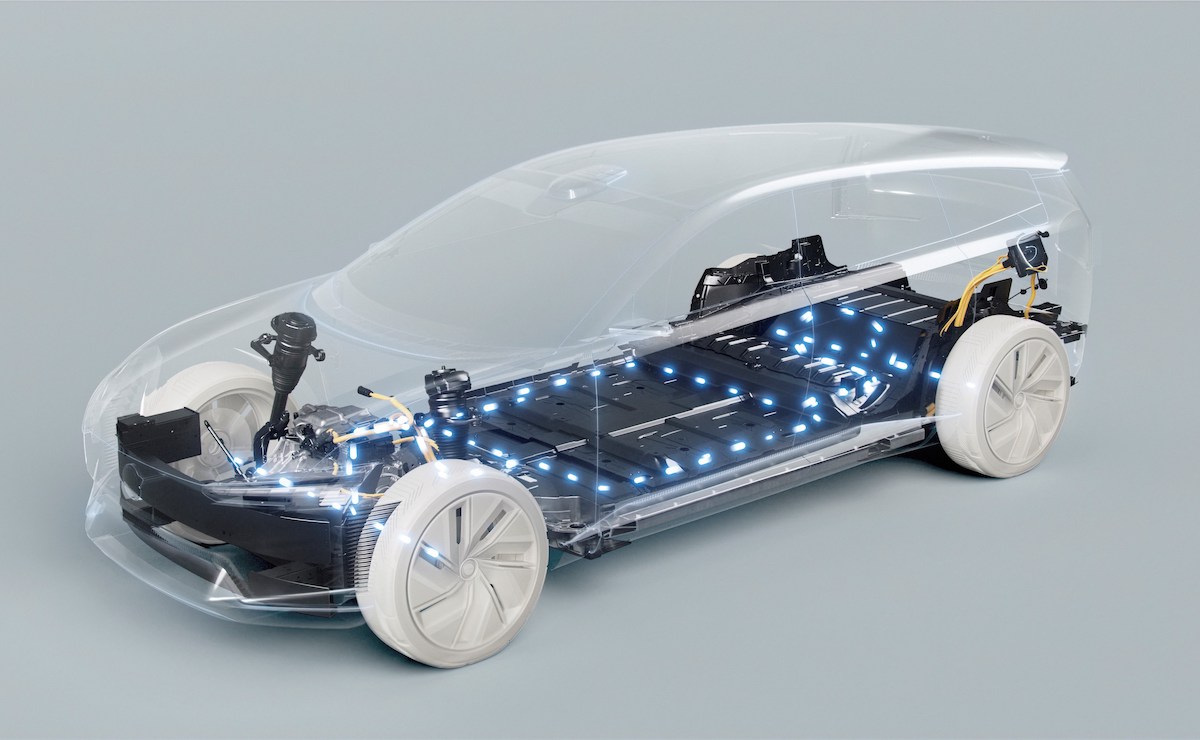
Of course, the star of tomorrow's electric car batteries will still be solid-state batteries. Compared to the liquid lithium-ion batteries mentioned above, solid metal lithium batteries have the inherent advantage of being safer (no electrolyte will flow out and cause a combustion risk); secondly, their most significant advantage is their high energy density, which can increase the vehicle range by 150%. At present, in addition to many battery manufacturers and R&D units, car manufacturers like Toyota, BMW, VW, and Hyundai are in this field of research with the fastest development progress. Toyota has even announced that it will launch the Lexus solid-state battery electric vehicle in 2020. Nevertheless, with the immature technology and high costs, I am skeptical that 2020 is a good time. The most significant difference in solid-state batteries is that the electrolyte is solid, and while ceramics are currently the dominant material, new polymers are being used to make lithium-ion transfer faster. However, the technical challenge is the higher operating temperature and the need to avoid a chemical accumulation of lithium metal in the negative electrode, which will reduce the electrochemical reaction area. Many of these technical hurdles are still in the way to mass production of solid-state batteries, so I think it will take another five years for the mature product quality. Then it will take another three to five years for the cost to be competitive.
In addition, there are many new battery technologies in the experimental stage, with Li-sulfur and Li-air batteries being the most aggressively developed; but until 2030, I believe that Li-ion and solid-state will be the main battery types used in commercially available EVs.