The topic of automotive supply chains has become familiar not only to the automotive industry but also to the general public in recent years. The reason is that the supply chain had not troubled traditional auto majors for a long time, but the chip shortage affected 8 million vehicles of global production last year, and this year is subject to an estimate of 3.3 million vehicles. Unable to fill a pile of orders to bring in cash, the decision makers of major automakers who used to be out of touch with reality are like cats on a hot tin roof, yet they don't know how to solve the predicament in front of them.
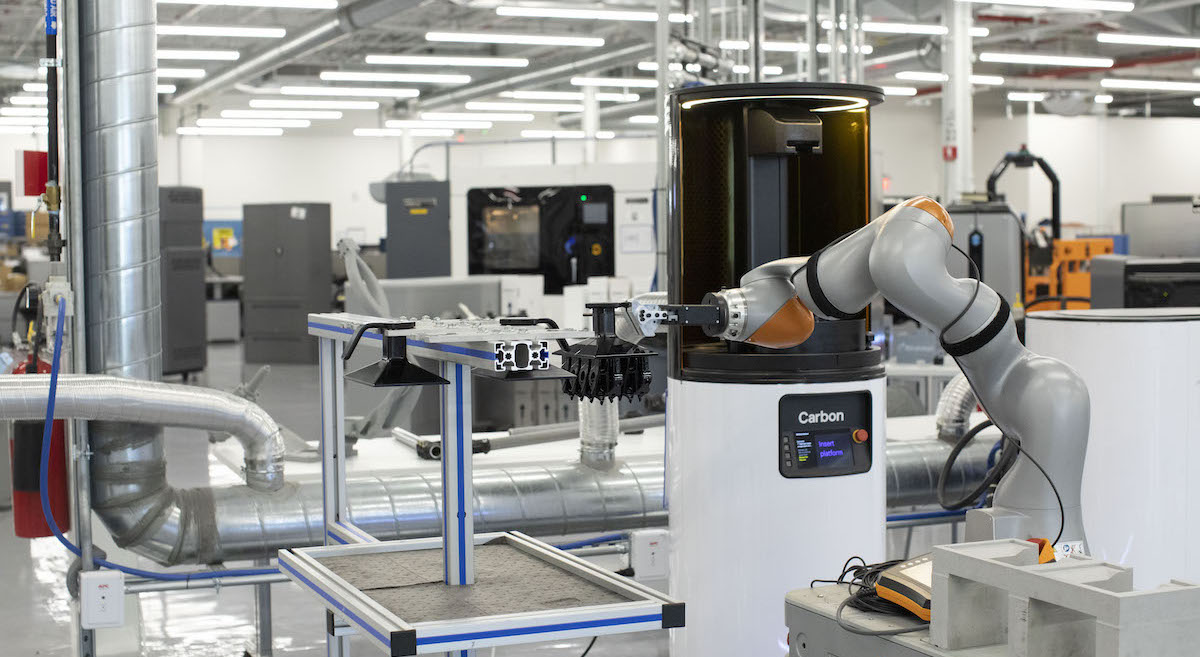
The shortage of microchips has no doubt caused the most serious problem to the supply chain in recent years, but as smart EVs are marching into the auto market, other problems such as power batteries and the battle for raw materials that extends upstream will directly affect the sales performance of the auto market in the future, not to mention the chaos in logistics and supply resulting from natural and man-made disasters such as pandemics and wars. In short, the most ideal solution for automakers is to become self-sufficient, designing and producing all key components by themselves, without interference from external factors. But none of the world's leading automakers have been able to pull it off so far. Nonetheless, at least in terms of battery supply, many financially strong automakers have built battery factories, either sole proprietorships or joint ventures (although the technology mostly comes from battery professionals), to meet the needs of their own future EV production lines. The devastating impacts of the disrupted supply chain on business operations have caused the "international division of labor" rule in the era of traditional fuel vehicles to begin to disintegrate in favor of an self-owned supply chain strategy as we enter the era of smart EVs. But for traditional automakers or startups that do not have the financial resources to support such a strategy, there are still several directions to consider…
- Form strategic alliances with Tier 1 and even Tier 2 suppliers or hold shares in each other. The subsystem of the vehicle is jointly designed, developed and manufactured with the vendors from the early design stage of the new model to ensure the stability of the supply of the key components. In other words, parts suppliers, who used to work as subordinates, must become horizontal partners to ensure the stability of the supply chain.
- The AI control chips for future smart cars or self-driving cars is so complex in design and so advanced in manufacturing process technology that it cannot be completed by automakers alone. It's a stark reality all automakers must face. Judging from the current situation, they either need to have a good relationship with the chip design majors or have to secure the supply from the foundry giants further upstream. Otherwise, "stocking up" will be the last resort, and the automakers must plan and undertake the resultant tied-up capital themselves in the long run.
- Product design for smart EVs is based on modulization, and many functional parts are designed and developed for common application to various models. The demand for the same parts will increase after mass production, allowing for greater flexibility in cost bargaining, future inventory management, and production volume adjustments for various models. Since "stocking up" is inevitable, automakers might as well amplify its advantages to counterbalance the disadvantages of the tie-up capital. Such a counterbalance is particularly important for multi-brand automotive groups. As for the concern about the lack of functionality or features differentiation between car models, let's leave it to the latest generation of E/E (electrical/electronic) architectures and OTA (over-the-air) updates!
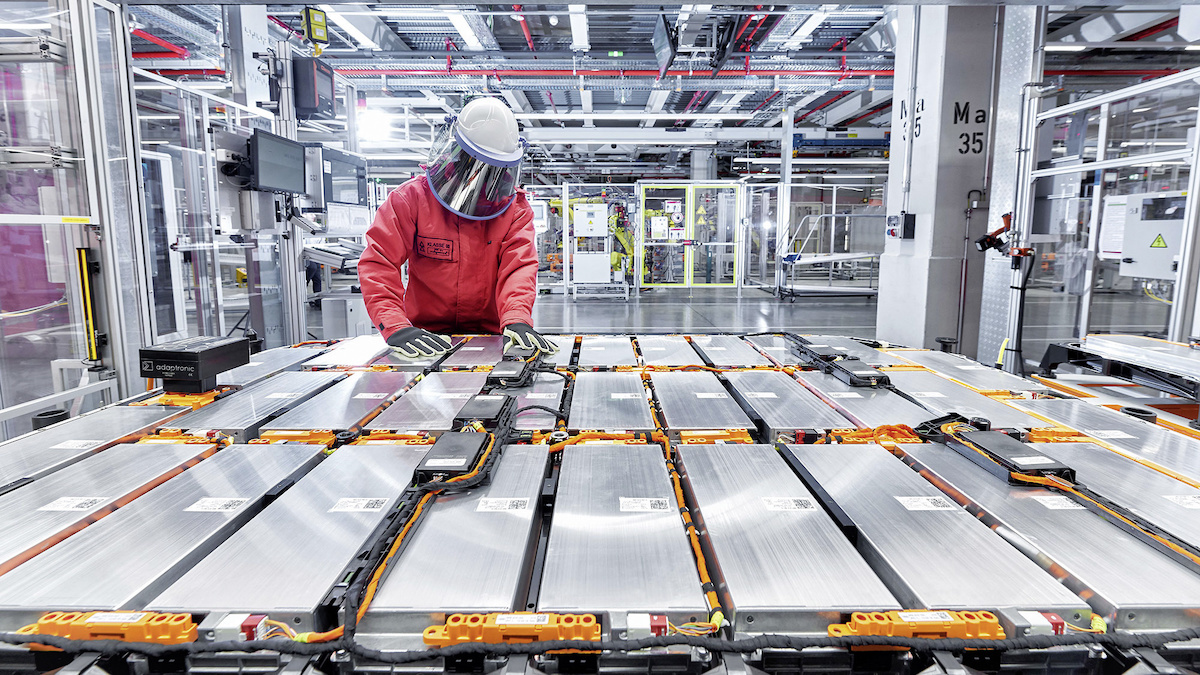
On the whole, the global automotive supply chain has evolved from the traditional, hierarchical supply chain with upstream and downstream responsibilities to the current "industry convergence" with automakers in the center of a radial (or parallel) partnership. The supply ecosystem will soon be centered on the needs of car owners and oriented toward value provision. Automakers and parts suppliers will have a networked relationship, and development resources will be flexibly earmarked according to market demand. At this stage, automakers will be forced to assign the leadership role in the design, development and production process to Tier One manufacturers. In other words, the design direction of new models will not necessarily be the sole decision of automakers in the future. The stability of supply chains will also be partly managed by Tier One manufacturers.